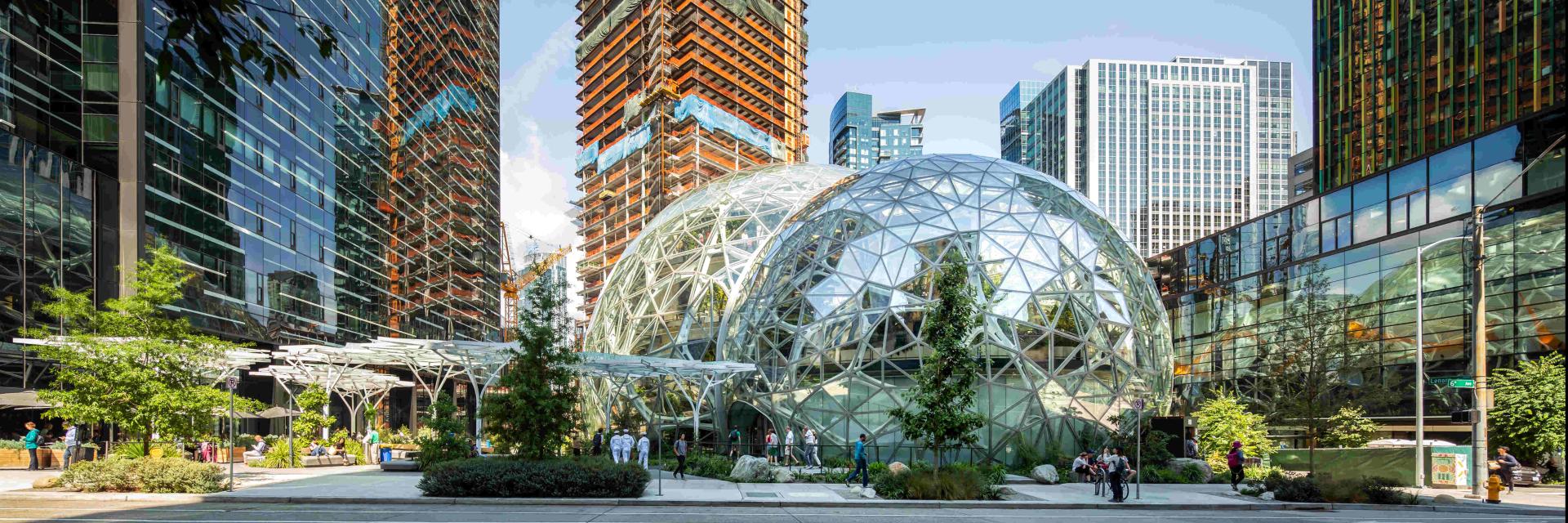
The Spheres building in Seattle is built with ECOPlanet low-carbon cement with 80% less CO2 inside.
Credit: NBBJGreen Cement
Power cement production with renewable energy and develop low-emission cement alternatives that sequester carbon and reduce industrial waste.
Cement is a binding element made of calcium, silicon, iron, and aluminum that is mixed with sand, gravel, and water to make concrete, the single most widely used building material in the world. Even though cement only constitutes 1 percent of concrete’s mass, it is responsible for 70 percent of carbon emissions from concrete manufacturing, mostly because cement-making is one of the most energy-intensive processes on earth. Cement production’s carbon emissions constitute at least 8 percent of the global total and exceed those of every country except the United States and China. The cement industry will need to decrease its annual emissions by at least 16 percent by 2030 to meet the Paris Agreement’s climate goals. Green cement is an alternate product that can lower cement production’s carbon emissions by up to 70 percent. Additional benefits include greater compressive strength, increased life expectancy, and utilization of industrial waste.
Action Items
Individuals
Learn about the impact of cement and concrete on greenhouse gas levels worldwide. Concrete is currently the most widely produced substance in the world, and it will soon outweigh all living matter. Concrete accounts for 70 percent of coastal and marine infrastructure worldwide. More than half of China’s coastline is concrete, as is 14,000 miles of the U.S. coastline. Between 2002 and 2021, the cement industry’s global emissions doubled from 1.4 billion tons to 2.9 billion tons, faster than most other carbon sources. Cement is used in almost every structure, including buildings, sidewalks, roads, bridges, and foundations.
- The production of Portland cement, the most common type, relies on baking limestone at high heat in kilns, often powered by fossil fuels, which releases carbon dioxide that otherwise would remain locked within the limestone for hundreds of millions of years. Producing a single kilogram of Portland cement releases a kilogram of CO2 into the atmosphere.
- The cement sector constitutes 7 percent of industrial global energy use, making it the third-largest industrial energy consumer.
- The cement industry produces an estimated 2 billion tons of carbon dioxide, three times the amount produced by the aviation industry. Burning coal accounts for 40 percent of the CO2 emissions, while limestone breaking down into lime within kilns accounts for the remaining 60 percent.
- In addition to carbon dioxide, cement plants emit more than 500,000 tons of sulfur dioxide, carbon monoxide, and nitrogen oxide annually.
- Each year the world produces about 4 billion tons of cement—1,200 pounds per person—with the potential to increase to 5 billion tons annually by 2050. 30 billion tons of concrete are used worldwide each year—triple the per capita demand compared to forty years ago. The demand for concrete is also increasing faster compared to other building materials such as steel or wood.
- Global concrete production could increase as much as 26 percent by 2050 based on projections that the number of buildings worldwide is expected to double by 2060.
Learn about green cement and its potential to lower greenhouse gas emissions worldwide. Green cement refers to cement that is either manufactured with the help of a carbon-negative process and/or made with alternative or recycled materials with lower embodied carbon emissions. It is designed to last longer than conventional concrete, reducing the need for replacement and repair. Some recent innovations in green cement include:
- Replacing the limestone in the traditional mine and grind concrete-making process with basalt or carbon-negative limestone, including algae-grown limestone, could reduce emissions by over 60 percent.
- Experiments using alternative cement materials have found that replacing cement with biochar, bioplastics (bio-based plastic polymers), agricultural waste, and animal wool not only lowers carbon emissions during production but also increases the soundproofing, water absorption, tensile strength, and carbon sequestration of concrete. See Biochar Nexus and Carbon Architecture Nexus.
- Researchers have prototyped cement that eliminates the CO2-releasing chemical reaction by using fly ash, a low-cost volcanic ash.
- Scientists from Harvard and MIT rediscovered the process behind the making of ancient Roman concrete, whose distinctive hot mixing step creates a final product that requires significantly less setting and curing time than modern concrete, a functional life span of thousands of years, and the ability to be used underwater.
- Researchers have created a type of living concrete that utilizes bacteria and sunlight, through photosynthesis, to create calcium carbonate that can cement sand particles together as it dries. The mixture can be poured into any shape, including bricks. The process absorbs carbon dioxide from the atmosphere and the resulting product is both durable and green.
Raise awareness about the negative environmental impacts of cement and the benefits of cement alternatives. Spreading the word about how current cement production accelerates global warming can help spur demand for cement manufacturers to invest in alternative cements and technology that lowers emissions.
- Connect with green cement advocates. Many green building forums provide opportunities to share resources and knowledge among those interested in using cement alternatives. See examples here and here.
- Contact your representatives. The Citizens’ Climate Lobby provides a step-by-step tutorial on how to write a letter to Congress as well as information on the benefits of clean energy that could power cement plants.
- Speak up. Write an op-ed for a newspaper or a social media organization advocating for green cement.
Groups
Construction Companies
Use less cement or use alternative materials that emit fewer greenhouse gases. The amount of cement within concrete can be reduced by 50–60 percent without affecting the strength of the concrete. In addition, the material within the cement can vary up to threefold without affecting performance. Replacing part of cement’s content with substitutes such as fly ash, slag, and rice hull ash, aerated mixes, biocements, and alternative cementitious materials like calcined clays reduce emissions by 50 percent. Find out more about the specific strengths of cement alternatives here and here.
- In Japan, Taiheiyo Cement Corporation has been developing “eco-cements” that replace large quantities of limestone with ash in order to limit carbon emissions.
- In Austria, Rieder has replaced 50 percent of the cement in its concrete panels with natural pozzolana (a material derived from volcanic ash), leading to a 30 percent reduction in CO2 emissions. By 2027, the company hopes to make its facade panel products cement-free.
Reuse concrete. Adapting circular construction, or the recovery and reuse of elements from past projects for new construction, could lead to reductions of up to 61 percent of greenhouse gas emissions emitted across buildings’ life cycles. In nonstructural applications, recycled concrete on-site also reduces costs by 50 percent in addition to reducing the volume of new concrete needed. If concrete cannot be reused and must be demolished, grinding it and spreading it thinly to maximize surface area and exposure to air allows it to absorb as much as 17 percent of the carbon dioxide emitted when its cement was manufactured.
- University of Tokyo scientists invented a concrete-making process that lowers greenhouse gas emissions by reusing old concrete products, using lower temperatures for manufacturing, and capturing carbon dioxide.
- Austrian cladding company Rieder opted for circular construction for its new headquarters by renovating a former bus garage and reusing concrete columns, recycled steel, and wooden walls, saving around 1,000 tons of CO2 in the process.
Cement and Concrete Manufacturers
Invest in innovative cement that reduces embodied emissions.
- CarbiCrete replaces the cement in its concrete with steel slag and injects carbon dioxide to produce calcium carbonates with higher compressive strength and better freeze resistance than traditional concrete.
- Solidia and LaFarge have developed a concrete mix design and curing process that mixes cement powder with sand and cures the mixture with carbon dioxide to create concrete with a 70 percent lower carbon footprint.
- CarbonCure has developed technology that injects captured carbon into wet cement, strengthening the material and locking in carbon dioxide. Using CarbonCapture’s technology, Amazon has saved an estimated 1,600 metric tons of carbon dioxide emissions thus far.
- Brimstone Energy is developing zero-carbon cement that replaces limestone with calcium silicate, which releases magnesium that absorbs carbon dioxide from the air.
- Cement manufacturer Block-Lite is partnering with climate tech startups Aircapture and Carbonbuilt to replace cement with an alternative mixture consisting of locally sourced industrial waste materials, which then will be cured with carbon dioxide pulled directly from the atmosphere.
- Colorado-based Prometheus Materials has developed a low-carbon cement alternative that replicates the structure of coral reefs by biomineralizing cyanobacteria grown using sunlight, seawater, and CO2, and has the potential to be mass-produced.
- Terra CO2’s technology partially replaces Portland cement with silicate from aggregate mines already in operation, leading to a 70 percent reduction in CO2 emissions for every ton of Portland cement replaced by the blend. The company is aiming to be able to completely replace Portland cement as well as transition to renewable energy within the next five years.
Join an industry-led initiative to lessen the environmental impact of cement and concrete production. Industry-led initiatives offer opportunities for cement companies to share important resources and knowledge about the development of green cement. Examples include:
- The Cement Sustainability Initiative is an international effort by twenty-four major cement producers that collectively account for 30 percent of the world’s cement production to minimize the impact of cement production and accelerate progress toward sustainable development.
- The ConcreteZero Initiative, a coalition of seventeen global businesses in the built environment sector, is aiming to accelerate the adoption of low-carbon concrete among concrete users. Businesses within the initiative have committed to using 30 percent low-carbon concrete by 2025, 50 percent by 2030, and 100 percent by 2050.
Research Institutes and Universities
Support the research and development of cement alternatives. Academic research has played a key role in the development of lower-carbon cement alternatives. Examples include:
- University of Tokyo researchers have developed the first process for cement made entirely from food waste such as tea leaves, orange peels, and coffee grounds. The cement, produced via a “heat pressing” used to make construction material from wood powder, has three times the tensile strength of existing concrete.
- In 2019, researchers at the National Taipei University of Technology and the Indian Water Resources Department discovered that agricultural and aquaculture farming waste could partially replace coarse and binding materials in concrete.
- Funded by a grant from ETH Zurich, Gnani Landrou developed a process that turns clay-based excavation materials into an alternative concrete that does not require cement. Inspired by homes in his native Togo, the mixture is two and a half times less expensive than cement and can be used to build floors and non-load-bearing walls.
- Researchers at the University of California, Irvine, and the University of Southern California have invented a process that grows minerals within a 3-D-printed structure inspired by the mantis shrimp, which could be scaled up to develop 3-D-printed, self-repairing concrete.
- Scientists at ETH Zurich have designed a 3-D-printed formwork made from recyclable mineral foam to create a precast concrete slab that uses geometry to preserve strength while reducing the amount of concrete needed by 70 percent.
- Worcester Polytechnic Institute researchers are using an enzyme found in red blood cells to create self-healing concrete that is four times more durable than traditional concrete, extends the life span of concrete-based structures, and prolongs the duration between repairs or replacements.
Governance
Mandate the use of lower-carbon cement in new construction. Governments can help lower carbon emissions from the cement sector by requiring that construction projects use less cement, cement alternatives, or cement produced in ways that release fewer emissions. Several governments at city, federal, and regional levels have already implemented such standards:
- Zurich, Switzerland, has required the use of carbon dioxide–reduced cement in new public buildings since 2013 and has mandated that all publicly owned buildings use recycled concrete since 2005.
- The UK government has mandated that the concrete used in the London Crossrail Project must have a cement-replacement content of at least 50 percent.
- Since 2015, the United Arab Emirates has required that all major infrastructure projects use cement that contains at least 60 percent blast furnace slag or fly ash.
- California has introduced legislation mandating that all cement used in the state must reach net-zero emissions by 2045.
- Hong Kong is building its first eco-shoreline using concrete bio-blocks designed by ECOncrete that mimic the intertidal zone to re-create habitats lost to land reclamation. By partially replacing the Portland cement with slag cement, the bio-blocks reach a pH close to that of seawater, which further helps to promote the growth of intertidal marine species.
- The U.S. Conference of Mayors passed a resolution at its annual meeting urging the use of carbon dioxide mineralized concrete for future city building and infrastructure projects.
- The European Union Waste Framework Directive requires 70 percent of construction waste to be reused.
Accelerate green public procurement practices to facilitate a shift to green cement. Six countries—the Netherlands, Sweden, Germany, France, the UK, and the United States—are in the vanguard of adopting low-carbon concrete and construction rules and green procurement policies.
- Here is a review of green public procurement programs for low-carbon concrete and construction.
Introduce financial incentives for companies to transition to green cement. Granting businesses incentives such as tax credits, reimbursements, or grants can help companies overcome the initial costs of transitioning to green cement ahead of the anticipated increase in concrete production.
- New Jersey has enacted a law granting businesses a tax credit worth up to 5 percent of a project’s total concrete costs if they use materials with low embodied carbon emissions, with an additional 3 percent credit granted to those that use concrete made with carbon capture, utilization, and storage technology.
- The Four Corners Carbon Coalition includes county governments in Colorado, Arizona, New Mexico, and Utah that are considering incentives to decarbonize cement and concrete.
Implement nature-based solutions in place of concrete where possible. As sea levels rise and global temperatures increase, hard concrete structures used for coastal defense are increasingly likely to break down and become less effective, leading to flooding in urban areas. Nature-based solutions such as seagrass meadows, mangrove forests, marshes, and coral reefs not only adapt more readily to sea-level rise but also serve as homes to marine species and act as carbon sinks. See Mangroves Nexus and Wetlands Nexus for more.
- Bio-based building materials such as wood, bamboo, straw, and hemp are being reformulated to be carbon-negative. Innovations in carbon-storing products, including engineered living materials such as biocements, bioplastics, and mycelium-based composites and insulation, are emerging. See Carbon Architecture Nexus.
Establish landfill taxes. Landfill taxes—environmental taxes paid in addition to landfill rates by entities that dispose of waste in landfills—help mitigate negative environmental impacts from waste disposal and have been shown to lower landfill rates. Since the tax is typically applied to construction waste, implementation could play a role in incentivizing coal and steel companies to process their waste materials for use in cement.
- To date, twenty-three EU member states, as well as Switzerland and the United Kingdom, have implemented landfill taxes. In-depth information on the tax specifications is published here.
- In 2021, New Zealand voted to increase its existing waste levy and expand its scope to include construction and demolition fills with the aim of reducing waste nationwide.
- Landfill taxes have also been implemented at the state level by several Australian states as well as the state of California, with the funds utilized to promote waste-reduction and recycling programs. The government of Canada published a Roadmap to Net-Zero Carbon Concrete by 2050 that outlines financial incentives and includes many of the approaches listed above.
Key Players
Organizations
Industrial Decarbonization Initiative (Global) is working to accelerate the shift of industrial organizations – both large and small – away from fossil-fuels.
World Green Building Council (Global) is WorldGBC’s global program working towards total sector decarbonization by 2050.
World Business Council for Sustainable Development (Global) brings together transformational organizations to form a global community that shifts the systems they work within towards a better future.
The Global Cement and Concrete Association (Global) is a trade group representing 80% of the world's concrete companies outside of China, with a vision of decarbonizing the industry as essential to deliver a sustainable future for the built environment.
The Cement Association of Canada represents five vertically integrated cement companies advocating for a net-zero industry.
Companies
Carbicrete (Canada) substitutes cement with steel slag, eliminating a highly polluting substance from the concrete mix, and replacing it with repurposed industrial waste.
ECOncrete (Israel) technology has helped engineers, architects, and asset owners build stronger, greener marine infrastructure.
EnGro (Singapore) is a leading provider of superior building materials, with more than 40 years of operational experience shaping landscapes in various parts of Asia, EnGro continues to maintain high standards of excellence for our products and services, and we look forward to contributing significantly to the industry and helping the industry go green.
Fortera (Global) has a patented transformation of cement manufacturing, designed to deliver a realistic pathway to zero CO2 cement production.
Holcim (Switzerland) creates cement that offers at least 30% lower carbon footprint with no compromise on performance.
Newtab-22 (UK) creates sustainable materials composed of natural, non-toxic ingredients and binders.
Prometheus Materials (U.S.) creates Zero-Carbon Bio-Cement and Bio-Concrete with 100% carbon reduction compared to traditional cement and concrete.
Rieder (U.S.) products utilize raw materials from nature, creating an authentic, honest material character.
Solidia (U.S.) combines low carbon processes, CO2 mineralization, and operational excellence to deliver superior concrete performance, strengthen supply chain resiliency, and reduce concrete's carbon intensity.
Terra CO2 (U.S.) provides high-performance, cost-competitive, and environmentally-friendly solutions for the global construction materials market.
Sublime Systems (U.S.) electrified manufacturing process makes low-carbon cement that makes no compromises.
Lafarge (Canada) makes ECOPact, a broad range of low-carbon concrete offering up to 90% lower emissions compared to standard concrete.
Individuals
Gnani Landrou is an inventor of an alternative clay-based concrete that does not require cement.
Kota Machida and Yuya Sakai are University of Tokyo researchers who developed the world’s first process for cement derived entirely from food waste.
Tiziana Vanorio is a Stanford University professor who is prototyping cement that eliminates the carbon dioxide–generating chemical reaction.
Wataru Kotaka and Ippei Maruyama are University of Tokyo researchers who pioneered a concrete-making process that lowers greenhouse gas emissions by reusing old concrete products.
Learn
Watch
How to Make Concrete Green! by Just Have a Think (13 mins.)
How We Could Make Carbon-Negative Concrete by Tom Shuler / TED (5 mins.)
What Is Green Concrete? How to Make Concrete Green by The Structural World (6 mins.)
Read
“Can the World’s Most Polluting Industries Decarbonize?” by Fred Pearce / Yale Environment 360
“Concrete” by Jeremy Gregory / MIT Climate Portal
“How Is Green Cement Better Than Regular Cement?” by Furqan Kabir / The Carbon Herald
“Solving Cement’s Massive Carbon Problem” by Mark Fischetti, Nick Bockelman, Wil V. Srubar / Scientific American
Listen
A Concrete Proposal: The Future of Eco-Friendly Architecture by Francisco Camacho / Planet Forward (15 mins.)
Researchers Are Trying to Find a Way to Cut Concrete’s Carbon Emissions by Nathan Rott / All Things Considered, NPR (3 mins.)
The Concrete That Helps the Climate by Martha Henriques / Future Planet (5 mins.)
Share this page